Limited by the quality of power batteries and cruising range, the lightweight of new energy vehicles has become the primary consideration of new energy vehicle companies. According to relevant statistics, every weight reduction of 100kg of new energy vehicles can reduce the battery cost by 20%. According to the latest "Energy Saving and New Energy Vehicle Technology Roadmap" released in China in 2020. The integrated design of the new energy vehicle powertrain is still the focus of development at this stage. As the integration of new energy powertrains becomes higher and higher, the proportion of the weight of the shell in the assembly is getting higher and higher. The light weight of the powertrain shell is of great significance to the improvement of the cruising range of new energy vehicles.
Magnesium is about two-thirds as dense as aluminum and less than a quarter as dense as steel or cast iron, making it one of the lightest metals used in engineering. In addition, it has a high specific strength and specific stiffness, good elongation and impact resistance, good machinability and dimensional stability, excellent electromagnetic shielding ability, and good material recycling. Therefore, magnesium alloy is an ideal lightweight material for new energy vehicles.
In recent years, magnesium alloys are mostly used in cockpit interior parts, such as steering wheel frames, instrument panel brackets and seat frames. These parts are mainly used in general environments, and the corrosion protection of magnesium alloys does not need to be considered. However, the electric drive assembly is located in the unenclosed space of the front cabin, and its service environment is a variety of atmospheric environments, with occasional salt water splash. Therefore, in addition to the protection of the magnesium alloy, the magnesium alloy electric drive assembly housing also needs to use
aluminum alloy bolts to solve the galvanic corrosion of the magnesium alloy housing and fasteners.
The use of aluminum alloy bolts is firstly to solve the problem of galvanic corrosion of magnesium alloy shells and fasteners. The oxidation resistance of a metal depends on the compactness of the oxide film formed by oxidation on its surface. The dense and continuous oxide film can restrict the passage of oxygen atoms, thereby inhibiting the internal metal from continuing to oxidize. The density coefficient α is the ratio of metal oxide to the volume of metal consumed to form the oxide. The α values of several commonly used metal elements are shown in Table 1. The density coefficient α of magnesium is 0.78. After being oxidized, a loose and porous oxide film is formed on the surface. Oxygen atoms can directly reach the substrate through the gaps in the oxide film and continue to oxidize. Therefore, the protective effect of the magnesium alloy oxide film on the substrate is limited, so magnesium alloys are not suitable in most corrosive environments.
Table 1 α of several commonly used engineering metal elements
Elements |
Cu |
Fe |
Ni |
Mg |
Al |
Zn |
Pb |
Sn |
Si |
α |
1.74 |
2.18 |
1.50 |
0.78 |
1.27 |
1.64 |
1.27 |
1.33 |
1.88 |
The chemical properties of magnesium are very active, and the standard electrode potential is -2.36V, which leads to poor corrosion resistance of magnesium alloys. In the electrolyte, magnesium is prone to serious galvanic corrosion as the anode, while the metal as the cathode does not corrode. Usually, magnesium alloy shells and fasteners are generally connected by dissimilar metals, which are prone to galvanic corrosion. The corrosion model is shown in Figure 1. The galvanic corrosion of magnesium alloy shells and fasteners is two reaction formulas, namely, the anodic reaction of magnesium and the cathodic reaction of other metals.
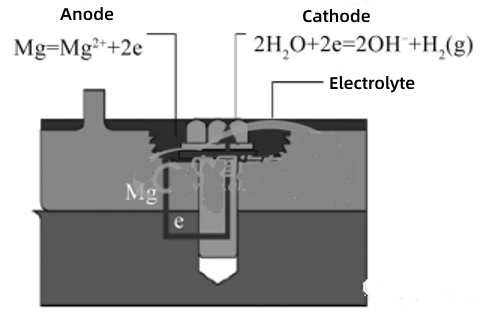
Figure 1 Galvanic corrosion models of magnesium alloy shells and fasteners
The galvanic corrosion current determines the speed of galvanic corrosion, and the galvanic corrosion current I can be expressed by the following formula.
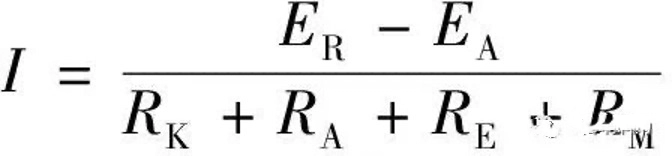
(1)
In the formula, EK and EA are the corrosion potentials of the cathode and anode. RK and RA are the polarization resistances of the cathode and anode. RE is the resistance of the electrolyte, and RM is the contact resistance of the cathode and anode metals. In general, RE and RK are much smaller than RA and RM, so Equation 1 can be simplified to Equation 2.
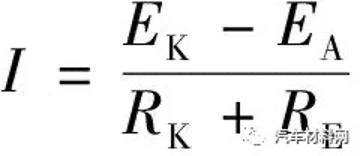
(2)
In the formula, EK and EA are the corrosion potentials of the cathode and anode. RK is the polarization resistance of the cathode, and RE is the resistance of the electrolyte. It can be seen from Equation 2 that the galvanic corrosion current increases with the increase in the corrosion potential difference between the cathode and anode metals. Magnesium acts as an anode, and the greater the potential difference between the metals in contact with it, the easier it is to cause corrosion. Some metals, such as iron, nickel and copper have a big potential difference from magnesium, which can cause great corrosion of magnesium. Other types of metal, such as aluminum, zinc, cadmium and tin have a smaller tendency to cause galvanic corrosion. According to this principle, the use of aluminum fasteners can reduce the galvanic corrosion with the magnesium alloy shell.
To compare the corrosion resistance of aluminum fasteners and steel fasteners in contact with the magnesium alloy shell, screw the aluminum bolts with EN AW-6056 design to the AZ91D magnesium alloy shell and soaked it in 1% NaCl solution for 100 hours. After the shell is tested, cleaned and dried, the corrosion situation is shown in Figure 2. In Figure 2(a), the aluminum alloy bolts and the magnesium alloy shell are well corroded, and pitting corrosion does not occur; in Figure 2(b), the steel bolts and the magnesium alloy shell have serious pitting corrosion.
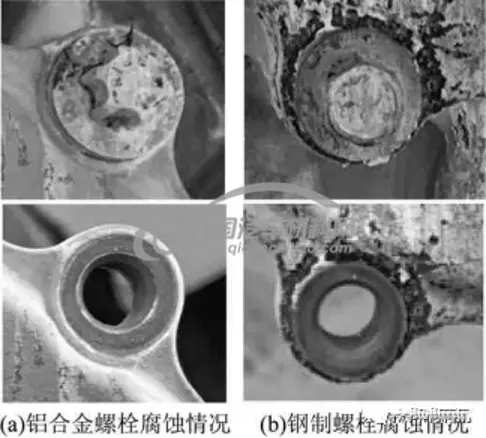
Figure 2 Galvanic corrosion tests of magnesium alloy shells and fasteners
(a) Corrosion of aluminum alloy bolts (b) Corrosion of steel bolts
Compared with steel bolts, in addition to fundamentally solving the electrochemical corrosion of magnesium alloy shells, aluminum alloy bolts with magnesium alloy shells have the following other advantages: (1) Each fastener can reduce 60% of the weight, and using it on the flange surface of the electric drive assembly can greatly reduce the weight of the assembly. (2) The thermal expansion coefficient of magnesium alloy and aluminum alloy is similar, and the thermal expansion coefficient of steel is about 1 time different. The threaded connection pair of steel bolts and magnesium alloy shells will generate additional stress due to temperature changes, often causing the compressive stress on the surface of the shell under the bolt head to exceed the compressive strength of the magnesium alloy, resulting in material creep on the surface of the magnesium alloy shell, and eventually leading to attenuation of the preload of steel bolts. The combination of aluminum alloy bolts and magnesium alloy shells is beneficial to eliminate or reduce thermal stress, reduce the creep of magnesium alloy shell materials, and improve the ability to maintain the preload (Figure 3). (3) The rigidity of the aluminum alloy is small, and the elongation corresponding to the same axial force and the tightening angle is great, so it is suitable to be tightened by the torque angles. When the connected parts are subjected to external loads, the alternating load on the bolts can be reduced. (4) The density coefficient of aluminum α is greater than 1, and an oxide layer can be formed on its surface to prevent corrosion. Therefore, aluminum alloy bolts do not require additional surface treatment.
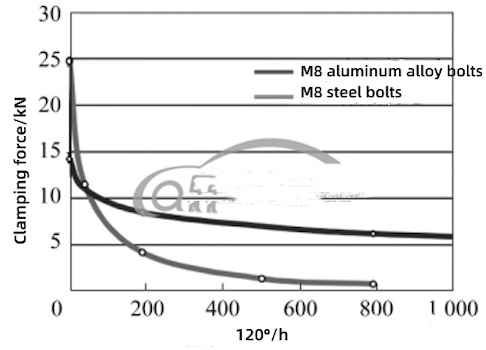
Figure 3 Clamping force retention of AZ91 magnesium alloy connected by aluminum alloy bolts and steel bolts
In addition to the use of aluminum alloy bolts, the counterbore structure that is easy to accumulate electrolytes should not be used at the joint connection as far as possible, and the use of a boss can further reduce the risk of galvanic corrosion of the magnesium alloy shell.